Understanding the Importance of Vacuum Pump Check Valves
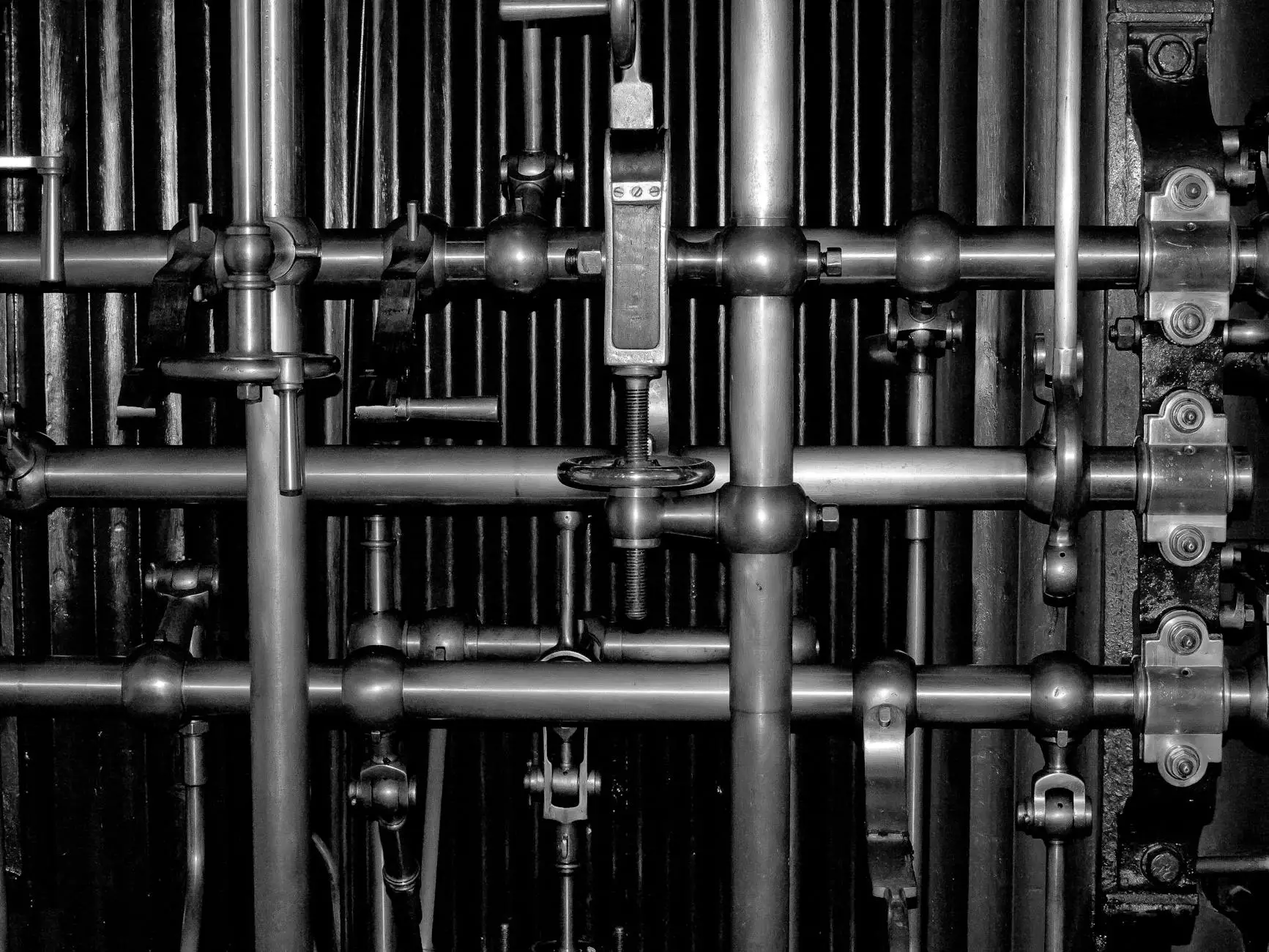
In the realm of vacuum technology, vacuum pump check valves serve as crucial components that ensure optimal system performance. For businesses engaged in manufacturing, research, and various industrial processes, understanding the function and importance of these valves can lead to increased efficiency and productivity. This comprehensive article aims to provide an in-depth analysis of vacuum pump check valves, their types, applications, and best practices for their use.
What is a Vacuum Pump Check Valve?
A vacuum pump check valve is a one-way valve that prevents backflow in a vacuum system. This is essential for maintaining the integrity of the vacuum, as any backflow can contaminate the system, hinder performance, and lead to costly downtime. The valve operates by using differential pressure; when the pressure is sufficient on one side, the valve opens, allowing flow in one direction and closing instantly when the pressure drops.
Types of Vacuum Pump Check Valves
There are several types of vacuum pump check valves, each designed to suit different applications and operational requirements:
- Ball Check Valves: Utilizing a spherical ball that seats against the valve body to prevent backflow. They are commonly used in low to moderate pressure systems.
- Spring-Loaded Check Valves: These use a spring mechanism to ensure a tight seal. They are ideal for high-cycling applications where quick response times are necessary.
- Poppet Check Valves: Featuring a disc that seals against a seat when back pressure occurs, providing a reliable option for vacuum systems needing high sealing performance.
- Diaphragm Check Valves: These use a flexible diaphragm to control flow. They are particularly beneficial in systems sensitive to contamination since they can offer a clean and reliable sealing method.
Key Benefits of Using Vacuum Pump Check Valves
Incorporating vacuum pump check valves into your system offers numerous advantages:
- Prevention of Backflow: Ensure that the vacuum is maintained by preventing backflow that can lead to contamination.
- Enhanced System Efficiency: By maintaining the appropriate pressure levels, these valves help optimize the overall performance of vacuum pumps.
- Durability and Reliability: Quality check valves are designed to last, minimizing maintenance and replacement costs.
- Versatility: Suitable for various applications ranging from laboratory settings to large-scale manufacturing, these valves are adaptable to many environments.
Applications of Vacuum Pump Check Valves
The applications for vacuum pump check valves are vast and varied. Here are some of the most common industries that rely on these essential components:
- Manufacturing: Used in systems for material handling, packaging, and assembly lines to ensure a consistent vacuum and protect products.
- Pharmaceuticals: Essential in maintaining sterile conditions during the processing and packaging of pharmaceutical products.
- Food Processing: Check valves are vital in vacuum sealing processes and for preserving freshness in food packaging.
- Research Laboratories: Critical for maintaining vacuum integrity in experiments and during the operation of sensitive analytical instruments.
Choosing the Right Vacuum Pump Check Valve
When selecting a vacuum pump check valve, several factors must be considered to ensure compatibility with your system:
1. Vacuum Level
Determine the maximum vacuum level your system will operate under. This ensures that the valve can withstand the operational conditions without failing.
2. Flow Rate Requirements
Assess the flow rate through the system. Each valve type has a different flow capacity; selecting the proper one will ensure that your operations run smoothly.
3. Compatibility with Fluids
Evaluate the fluids that will be passing through the valve. Ensure that the materials used for the valve construction are resistant to any chemicals or corrosive substances.
4. Temperature Conditions
Consider the operating temperature of your vacuum system, as different valve materials have varied temperature tolerances.
Maintenance Tips for Vacuum Pump Check Valves
Proper maintenance of vacuum pump check valves is crucial for ensuring their longevity and reliability. Here are some tips:
- Regular Inspections: Schedule routine checks to ensure valves are functioning correctly and free from blockages.
- Seal Condition: Inspect seals for signs of wear or damage. Replace any worn components promptly to prevent leaks.
- Cleaning: Keep the valves clean from debris and contaminants that could impede their operation.
- Lubrication: If applicable, ensure that moving parts are appropriately lubricated to facilitate smooth operation.
Integrating Vacuum Pump Check Valves into Your System
Proper integration of vacuum pump check valves into your vacuum system is essential for maximizing their effectiveness:
- Placement: Install the valve as close to the vacuum pump as possible to minimize the risk of backflow.
- Orientation: Ensure that the valve is oriented correctly according to the manufacturer's instructions to prevent operational issues.
- Testing: After installation, conduct a thorough test of the system to ensure that the valve operates correctly under various conditions.
The Future of Vacuum Pump Check Valves
The future of vacuum technology holds exciting advancements, and the role of vacuum pump check valves will likely evolve:
As manufacturing processes advance and move towards automation, the demand for more sophisticated vacuum systems will grow. This includes valves that not only prevent backflow but also integrate smart technology for monitoring and diagnostics. Enhanced materials will lead to valves that offer even greater resistance to wear and corrosive elements, thus extending their service life and reliability.
Final Thoughts
Understanding and implementing vacuum pump check valves in your vacuum systems is essential for maintaining efficiency and operational integrity. By choosing the right type and ensuring they are properly maintained, businesses can reap the benefits of enhanced performance and productivity. Whether you are looking to buy membranes, silicone membranes, rubber membranes, vacuum system parts, or natural rubber membranes, consider integrating quality check valves from reputable suppliers.
Your business deserves the best vacuum technology to ensure peak operation, so invest wisely in your components, prioritizing quality and efficiency at every turn. For more information, visit vacuum-presses.com to discover a range of solutions tailored to your needs.