The Transformative Role of Injection Molded Plastic Parts in Contemporary Manufacturing
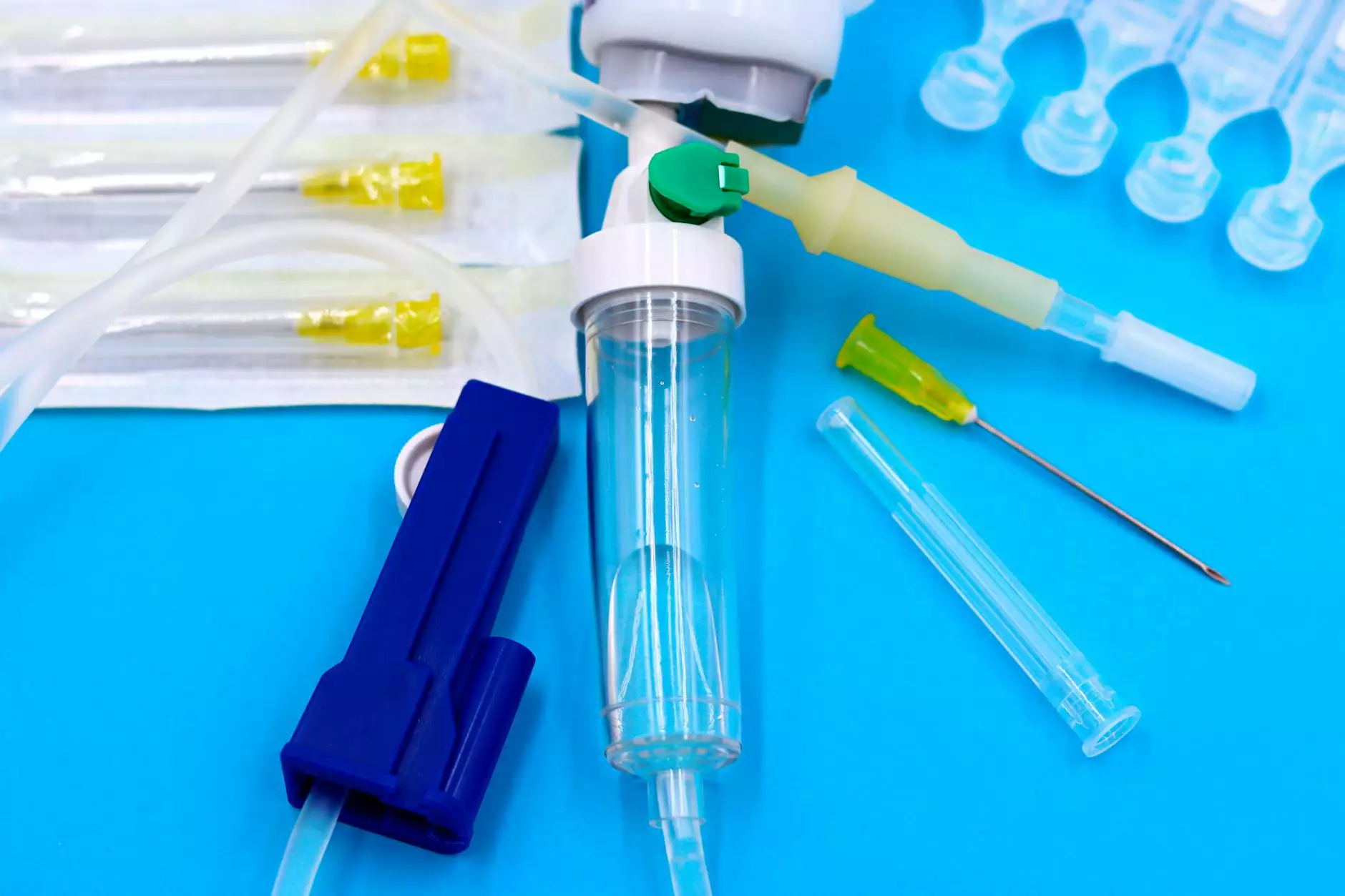
In today's rapidly evolving manufacturing landscape, injection molded plastic parts have emerged as a revolutionary component, streamlining production processes and enhancing product quality. This technique, pivotal across various industries, merges precision with efficiency, making it a cornerstone of manufacturing practices. In this detailed exploration, we will delve into the nuances of injection molding, its benefits, applications, and how businesses like Sumiparts leverage this technology to provide unparalleled industrial solutions.
Understanding Injection Molding: A Brief Overview
Injection molding is a manufacturing process where molten material, typically plastic, is injected into a mold under high pressure. This method allows for the creation of parts with complex geometries and intricate details, catering to diverse industry needs. Below are the key components involved in the injection molding process:
- Injection Unit: Prepares and injects the melted plastic into the mold.
- Mold: The hollowed-out block where the liquid plastic is cooled and solidified into the desired shape.
- Clamping Unit: Holds the mold tightly during the injection process to prevent leakage.
Why Choose Injection Molded Plastic Parts?
Injection molded plastic parts offer several advantages that make them a preferred choice in manufacturing. Below are some of the primary benefits:
1. Cost-Effectiveness
Cost savings are one of the foremost advantages of injection molded plastic parts. The initial setup costs, including the creation of molds, might seem high. However, once established, the process yields high volumes of parts with minimal labor costs, significantly reducing the cost per unit.
2. High Efficiency and Precision
Injection molding provides exceptional precision. The molds are created with advanced technology, ensuring that each piece is manufactured to exact specifications. This level of accuracy minimizes the need for post-manufacturing adjustments, thus enhancing overall productivity.
3. Versatility of Materials
A wide range of plastic materials can be used in the injection molding process, including but not limited to:
- ABS (Acrylonitrile Butadiene Styrene)
- Polyethylene
- Polypropylene
- Polycarbonate
This versatility allows manufacturers to select materials best suited for their product's requirements regarding durability, flexibility, and thermal resistance.
4. Complex Geometries and Designs
The capability to create intricate designs sets injection molding apart from other manufacturing methods. Manufacturers can produce parts that contain complex features, helping innovate product designs that can cater to specific functions or aesthetic results.
5. Enhanced Strength and Durability
Injection molded parts tend to exhibit superior structural integrity compared to those manufactured through methods like machining or welding. This is due to the uniform distribution of plastic and the minimal voids within the final product, enhancing its performance in demanding applications.
Applications of Injection Molded Plastic Parts
The applications of injection molded plastic parts are vast and span multiple industries. Here are some of the prominent sectors where injection molding plays an indispensable role:
1. Automotive Industry
In the automotive sector, components such as dashboards, interior trims, and housing for electrical fixtures often utilize injection molded plastics. The lightweight and durable characteristics contribute to overall vehicle efficiency and performance.
2. Consumer Electronics
Electronics devices require parts that not only fit perfectly but also endure rigorous usage. Injection molded parts are found in devices like smartphones, laptops, and gaming consoles, where precision and aesthetics are crucial.
3. Medical Devices
In healthcare, the use of injection molded components is critical for medical devices like syringes, inhalers, and various diagnostic equipment. The consistency and sterilizability of these parts are vital for patient safety.
4. Household Products
Everyday items such as containers, cleaning supplies, and kitchen appliances leverage injection molded parts for functionality and design, promoting usability while ensuring cost efficiency.
5. Industrial Components
For industrial applications, injection molded parts are used in machinery housings, gears, and fixtures. Their durability ensures prolonged operational life and reduced maintenance costs.
Injection Molding Process: A Step-by-Step Guide
The injection molding process can be broken down into several stages, each critical to producing high-quality plastic parts:
- Material Preparation: Resin pellets are dried and heated to the correct temperature.
- Injection: The molten plastic is injected into the mold.
- Cooling: The material is allowed to cool and solidify within the mold.
- Mold Opening: Once solidified, the mold opens, and the part is ejected.
- Finishing: Any secondary processes, such as trimming or painting, are performed.
Environmental Considerations and Sustainability
As industries advance toward sustainability, the injection molding sector is also evolving. Manufacturers are increasingly exploring recyclable materials and eco-friendly practices. By using biodegradable plastics and optimizing processes to reduce waste, companies like Sumiparts aim to contribute positively to environmental sustainability.
Your Partner in Quality and Precision: Sumiparts
At Sumiparts.us, we pride ourselves on being at the forefront of industrial manufacturing. Our expertise in injection molded plastic parts aligns with our commitment to delivering high-quality products that meet rigorous industry standards. With an extensive range of services—including machining, laser cutting, and welding—we offer comprehensive solutions tailored to your specific needs.
Our state-of-the-art facilities are equipped with advanced technology to ensure precision, efficiency, and reliability in every project. By partnering with us, you’ll benefit from our vast industry experience and steadfast dedication to customer satisfaction.
Conclusion: The Future of Injection Molded Plastic Parts
As we look ahead, the future of injection molded plastic parts appears promising. With continuous advancements in materials and processes, the industry is poised for significant growth, driving innovation in product design and manufacturing efficiency. Companies like Sumiparts are essential players in this transition, pushing the boundaries of what is possible in industrial supply chains.
Whether you are exploring options for mass production or specialized parts, understanding the benefits and applications of injection molding can help you make informed decisions. Embrace the transformative potential of injection molded plastic parts and partner with industry leaders to achieve excellence in manufacturing.